What is AISI 4130 ?
AISI 4130 is a medium carbon, low alloy steel material specified in standard ASTM A29. AISI 4130 is a low-alloy steel known for its high strength, toughness, and good weldability, making it widely used in oil & gas, aerospace, and automotive industries.
AISI 4130 Chemical Composition
Grade | C | Si | Mn | P | S | Cr | Mo |
4130 | 0.28-0.33 | 0.15-0.35 | 0.4-0.6 | ≤0.035 | ≤0.04 | 0.8-1.1 | 0.15-0.25 |
Equivalent material with AISI 4130
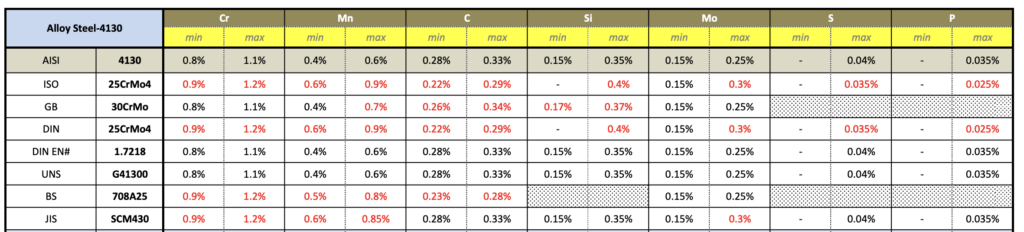
Mechanical Property of AISI 4130
roperties | Metric | Imperial |
---|---|---|
Tensile strength, ultimate | 560 MPa | 81200 psi |
Tensile strength, yield | 460 MPa | 66700 psi |
Modulus of elasticity | 190-210 GPa | 27557-30458 ksi |
Bulk modulus (Typical for steel) | 140 GPa | 20300 ksi |
Shear modulus (Typical for steel) | 80 GPa | 11600 ksi |
Poissons ratio | 0.27-0.30 | 0.27-0.30 |
Elongation at break (in 50 mm) | 21.50% | 21.50% |
Reduction of area | 59.6 | 59.60% |
Hardness, Brinell | 217 | 217 |
Heat Treatment for AISI 4130
Normalizing
- Process: Heat to 870–925 °C (1600–1700 °F), then air cool.
- Purpose: Refines grain structure, improves toughness, relieves internal stresses.
- Application: Used when a balance of strength and ductility is needed.
Annealing
- Process: Heat to ~790–850 °C (1450–1560 °F), then furnace cool slowly.
- Purpose: Softens the steel, improves machinability, relieves stress.
- Application: For pre-machining or forming; not typically used in final parts for high-pressure service.
Hardening (Quenching) + Tempering
- Process:
- Hardening: Heat to ~870–900 °C (1600–1650 °F), hold, then quench in oil or water.
- Tempering: Reheat to 400–650 °C (750–1200 °F), hold, then air cool.
- Purpose: Increases strength and hardness while controlling brittleness.
- Application: Common in pressure-containing components like API 6A flanges, fittings, and tubing.
Stress Relieving
- Process: Heat to ~540–650 °C (1000–1200 °F), hold for 1 hour per inch of thickness, then cool slowly.
- Purpose: Minimizes residual stress after welding or machining.
- Application: Often applied after fabrication before final inspection/testing.
Application of AISI 4130
AISI 4130 steel finds many applications as forgings for the aerospace,oil and gas,automotive, agricultural and defense industries etc.
Typical applications for 4130 steel uses include:forged valve bodies, pumps,Aircraft engine mounts,Welded tubing,fittings,Hydraulic tools,etc
AISI 4130 Round Bar
Length: 3 to 6 meters (or custom cut-to-length)
Diameter: 10 mm to 500 mm (3/8” to 20”)
AISI 4130 Flanges
AISI 4130 flanges are forged flanges according to API 6A standard,which is made from a low-alloy steel containing chromium and molybdenum, offering an excellent combination of strength, toughness, and weldability. These flanges are especially popular in the oil & gas industry, particularly for high-pressure and sour service (H₂S) applications
AISI 4130 is the equivalent grade of 25CrMo4
About 25CrMo4
25CrMo4 is a low-alloy chromium-molybdenum steel grade, similar to AISI 4130, and widely used in applications requiring high strength, good toughness, and resistance to wear and fatigue. It’s standardized under EN 10083-3 and used across industries like automotive, aerospace, pressure vessels, and oil & gas.
25CrMo4 Chemical Composition
Chemical composition % of steel 25CrMo4 (1.7218): EN 10083-3-2006
C | Si | Mn | P | S | Cr | Mo |
0.22 – 0.29 | max 0.4 | 0.6 – 0.9 | max 0.025 | max 0.035 | 0.9 – 1.2 | 0.15 – 0.3 |
Mechanical properties of steel 25CrMo4 (1.7218)
Nominal diameter (mm): | to 16 | 16 – 40 | 40 – 100 | 100 – 160 | 160 – 330 |
Rm – Tensile strength (MPa) (+QT) | 900-1100 | 800-950 | 700-850 | 650-800 | 600 |
Heat Treatment of 25CrMo4
- Normalizing: ~880 °C, air cooled
- Quenching: ~850–900 °C, followed by oil/water quenching
- Tempering: 500–700 °C, depending on required hardness/strength
- Can be quenched & tempered to achieve high yield strength similar to 4130