Surface Treatment solution for Stud Bolts
Stud bolt,as the fastners,are widely used in many industrial,it is called the rice grain of the industrial, Moreover, the quality and reliability of fasteners directly influence the stable operation of the entire industrial system.
With the exception of structures of weather resistant steel (WRS), the long – term corrosion protection to bolt groups in structures is given by the full coating system, applied after installation. (For WRS steel structures the bolts, nuts and washers should be of WRS material and are not given any protective treatment,
Threaded components are difficult to blast clean effectively after installation, and even more difficult to metal spray effectively, because of the high surface cleanliness required.
So The surface coating on a fastener is as important as the underlying fastener material. Fastener threads are manufactured in a cutting or forming machining process, and the surface coatings add an essential layer of protection to the fastener shank and threads
Choosing the right surface treatment for stud bolts depends on factors such as corrosion resistance, temperature, and environmental exposure. Below are the most common surface treatment options.(HDG,PTFE XYlan,ZINC Plating)
Black Oxide (Blackening)
- Standard: ASTM D769
- Process: Oxidation of iron surface
Black iron oxide plating which is more commonly known as black oxide, for example this chemical process will create a thin coat of black type-II high quality finish specification coating on the external surface of steel bolts For its anti-rust grade,
Phosphate Coating (Manganese or Zinc Phosphate)
- Standard: ASTM D769
- Process: Chemical conversion coating
- Coating Thickness: 2–15 µm
In this process, a phosphate layer is formed on the surface of bolt and can have two purposes as basic for further coating or be intended to serve alone as protection. The main purpose of phosphating is to enhance paint adhesion and thereby corrosion protection. Stud Bolts are placed in a phosphoric acid bath that uses the metal as an improved third structure to grow insoluble crystalline phosphates.
Zinc Electroplating (Cold Galvanizing)
- Standard: ASTM B633
- Process: Electrolytic deposition of zinc on the surface
- Coating Thickness: 5–25 µm (0.2–1 mils)
Electrogalvanizing is a process in which a layer of zinc is bonded to steel to protect against corrosion, enhance adhesion, or give an aesthetic appearance.
Compared to hot-dip galvanization, electrogalvanization offers these significant advantages:
- Lower thickness deposits to achieve comparable performance
- Broader conversion coating availability for increased performance and colour options
- Brighter, more aesthetically appealing deposits
Hot-Dip Galvanizing (HDG)
- Standard: ASTM A153 / ASTM F2329
- Process: Dipping the stud bolts in molten zinc (450°C)
- Coating Thickness: 43–86 µm (1.7–3.4 mils)
Bolts and nuts are dipped in molten zinc and then centrifuged to remove excess zinc. Such products are commonly referred to as spun galvanized.
Hot dip galvanizing provides the highest level of corrosion protection as it gives a considerably thicker coating than either sherardizing or electroplating. It is also one of the two methods preferred by the Specification for Highway Works.
Cadmium Plating (for Aerospace & Military Use)
- Standard: ASTM B766
- Process: Electroplating with cadmium
- Coating Thickness: 5–25 µm
Cadmium plating, also known as cadmium electroplating, is a type of metallic coating that has distinct and useful properties. Cadmium plating is typically used in the aerospace industry and other environments exposed to high salt concentrations, and is usually paired with substrate materials such as steel, copper, various types of iron, and powdered metals.
ZINC Nickel Plating
- Standard: ASTM B689
- Process: Electroplating with Zinc nickel alloy
- Zinc nickel plating is a type of metal finishing process that deposits a layer of zinc-nickel alloy onto the surface of a substrate. In this alloy, the nickel content usually falls between 12-16 wt%, though it can vary between 10-18 wt% based on specific requirements.
Fluoropolymer Coatings (PTFE / Xylan / Teflon)
- Process: Base coating+Spray process + heat curing
- Coating Thickness: 15–30 µm
PTFE (polytetrafluoroethylene) Coatings are another name for Fluoropolymer, Xylan™, or Teflon™ coatings. PTFE and fluoropolymer coatings are often used in corrosion management because of the tough qualities due to the strong carbon-fluorine bonds.
Comparing above the coating surface,Fluoropolymer Coatings has the most strong anti-corrosion performance,it can be used for offshore,marine enviorement because of below character
Abrasion and Wear Resistance.
Corrosion Resistance
Chemical Resistance
Low Friction
Anti-Galling and Seizing
How to Choose Right Surface Treatment for Your Fasteners
This table compares different surface treatments based on cost, corrosion resistance, and best applications to help select the right option for your specific needs.
Surface Treatment | Cost | Anti-Corrosion Performance | Applications |
Hot-Dip Galvanizing (HDG) | $$ | ⭐⭐⭐⭐ (Excellent) | Offshore, Marine, Industrial, Structural Steel |
Zinc Electroplating | $ | ⭐⭐ (Moderate) | Automotive, General Industrial, Low-Corrosion Areas |
PTFE / Xylan Coating | $$$$ | ⭐⭐⭐⭐⭐ (Superior) | Oil & Gas, Petrochemical, Offshore, High-Temp |
Cadmium Plating | $$$ | ⭐⭐⭐⭐ (Excellent) | Aerospace, Military, Offshore, High-Lubricity Needs |
Blacken | $ | ⭐ (Low) | Automotive, Machinery, Appearance Enhancement,indoor |
Zinc Nickel Plating | $$$$ | ⭐⭐⭐⭐ (High) | Aerospace, High-Temperature, Marine, Corrosive Environments |
performance comparison sheet between different coatings
You may find the salty spary duration for different coatings on fasteners as below
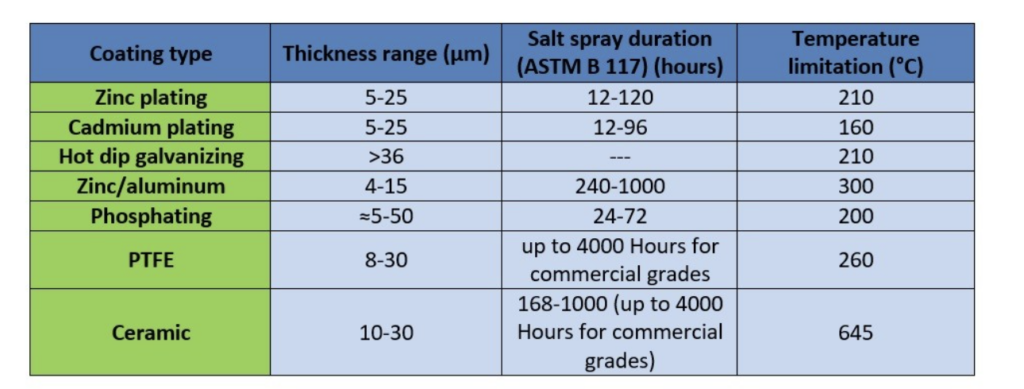